The Challenge
A global financial services firm had recently acquired a 1.1 million sq. ft. office space at Nirlon Knowledge Park, Mumbai. With a fast-approaching move-in timeline and corporate fit-out teams mobilizing, the client urgently needed to begin interior design planning. However, a critical roadblock emerged as the As-Built drawings received from the base builder were unreliable and outdated.
Several inconsistencies were noticed between the documented services and actual site conditions, particularly in slab cutouts, shaft locations, and ceiling heights. This posed a major risk to the project’s success any errors carried over into the fit-out phase could lead to rework, structural mishaps, and costly delays.
Client’s Initial Hurdles
- The as-built drawings were outdated and inaccurate, leaving the design team without a dependable foundation.
- With just eight weeks before interior work began, time was too short for conventional survey methods.
- Accurate PT slab markings were essential a single error could compromise safety.
- Multiple levels, ceiling variations, and concealed services made quick, precise documentation critical.
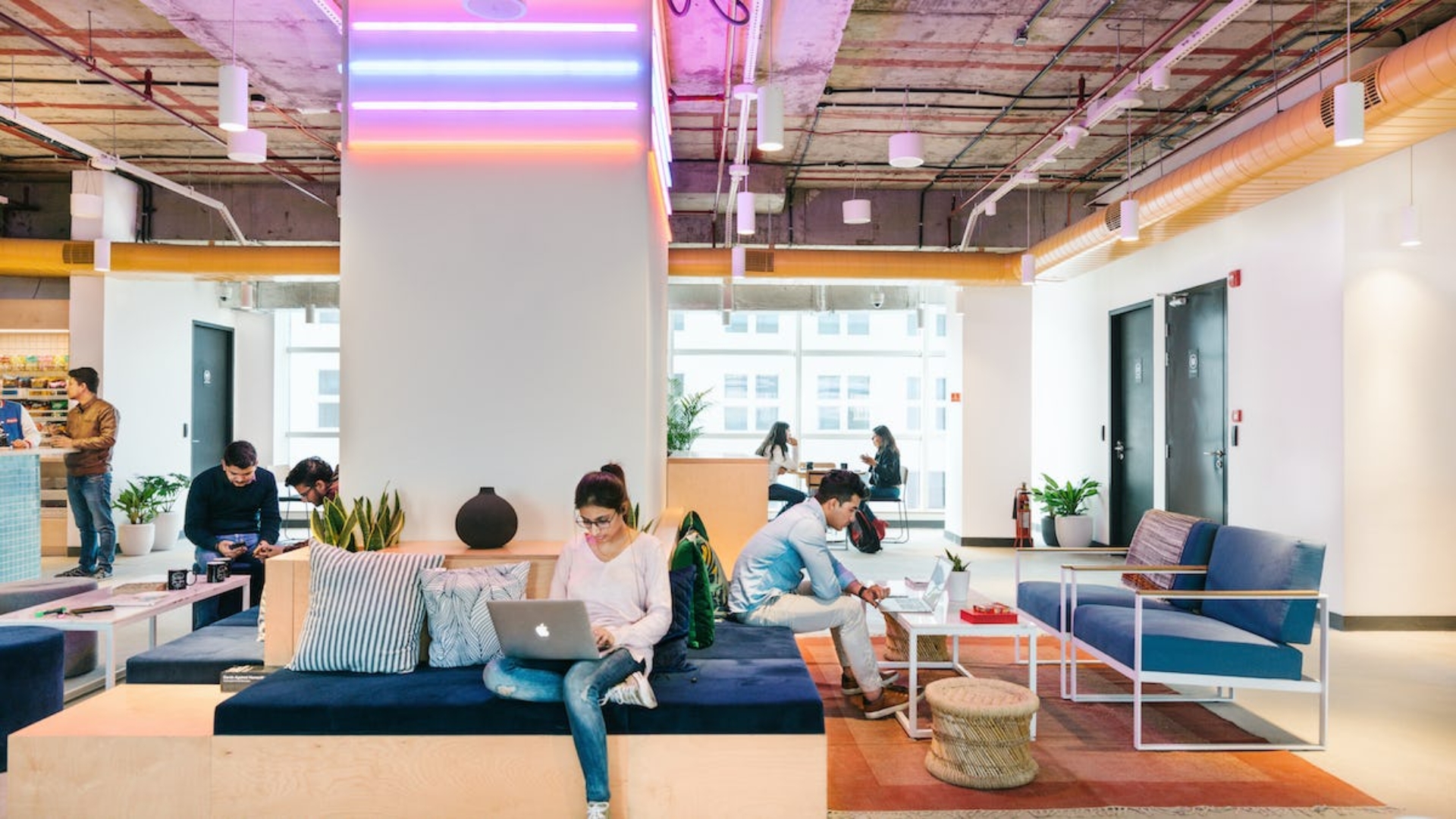