Introduction: Physical libraries and their impact on cost and time in operation.
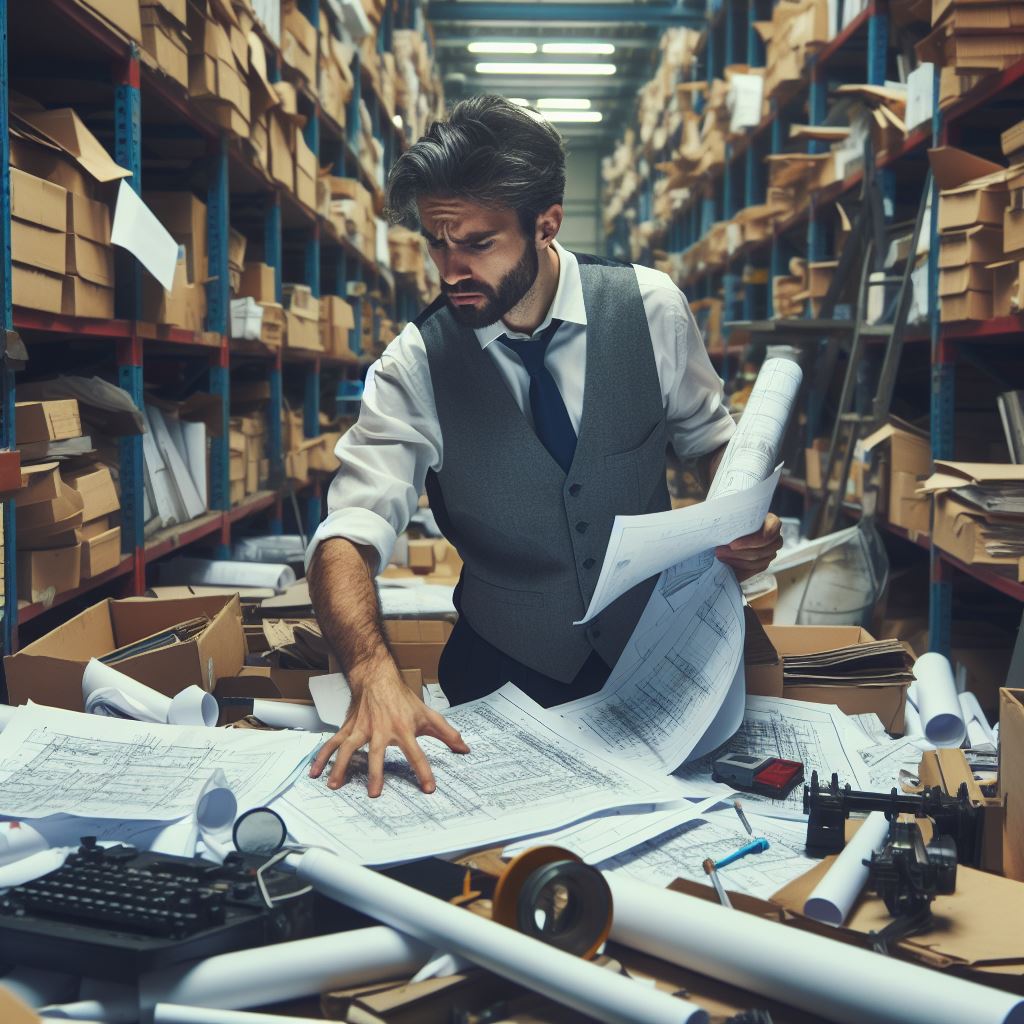
In large manufacturing units, there are physical libraries where all the technical documents (engineering drawings, user manual, spec sheets, QC certificates, Inspection documents, etc) are stored. There is also a custodian for all these drawings called librarians who keep track of these documents as well. He will be well aware of all the documents available in the library.
Usually, these documents are accessed by the maintenance/engineering or operating departments during 4 or 5 instances as mentioned below.
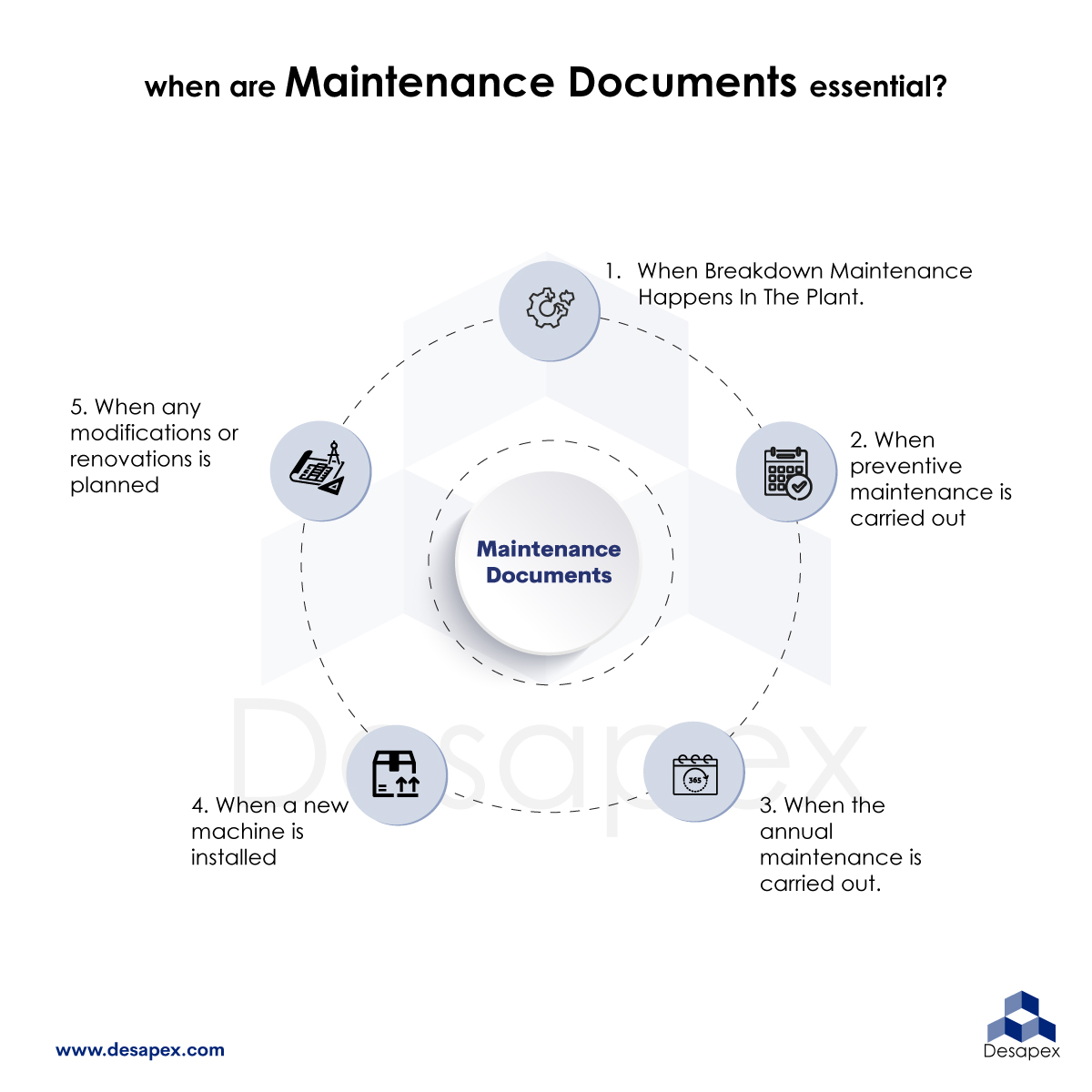
When these departmental people gain more experience working in the same plant the number of times they refer to these documents decreases.
But have you ever thought of a library without a librarian? Yes, it will be a mess. Here is something for you to think of. Consider a librarian who will be there in that organization for 30-40 years. He/She is well aware of the changes happening in that unit and where each document is stored. What if he is retiring and has to hand over the charge to the next person? I am sure that the new person won’t be able to find the documents on time at the time of a breakdown.
Another best part is practically speaking there won’t be a librarian who looks after the library in the majority of the industries. Usually, all these documents will be with the maintenance or engineering department. It will be disordered; they will also take time to find the relevant documents at the time of emergency. There is a potential impact on cost and time when an operation stops in a manufacturing plant which gives additional pressure to meet the planned production.
Operation halts in manufacturing impacts cost and time, straining planned production
Now let’s see how a Common Data Environment(CDE) can be helpful to the maintenance/ engineering and operations departments in a manufacturing industry.